The Poulan model 3400, 3700, 3800 and 4000 chainsaws are undervalued. They are a professional grade chainsaw and in many ways ahead of their time when introduced in 1979.
They all share the same crankcase and crankshaft with different diameter pistons and cylinders for different displacement. With a little searching, it isn’t hard to find a good used one for less than $150. I thought it would be a good learning experience to modify the crankshaft and increase the stroke for an increase in performance. The stock crankshaft stroke is 33.5mm. I checked runout of the stock crankshaft to establish a baseline tolerance. The stock crankshaft has about .0002″ runout when checked on V blocks. There is a better way to check runout. More on that later.
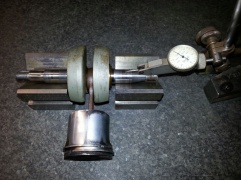
The crankshaft has been disassembled.
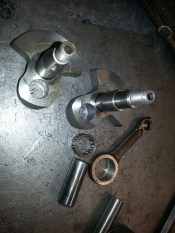
The “cheeks” have been removed. 4140 plates have been ground, tack welded and bored. The new stroke will be 41mm, and increase of 7.5mm. 41mm is the most that will fit within the crankcase.
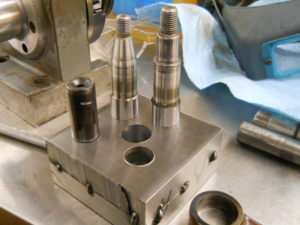
The crankcase needs to be bored to accommodate the additional stroke.
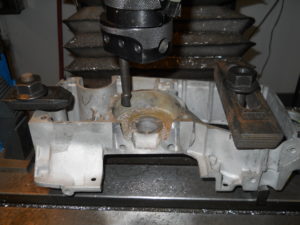
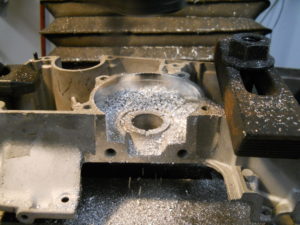
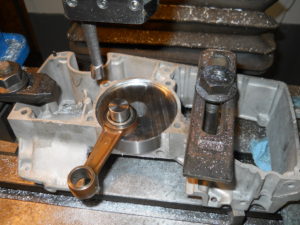
Boring the crankcase created a problem. I bored through the case, into screw pockets. To solve this problem, I made steel spacers for longer screws and filled the cavity with pour able polyurethane.
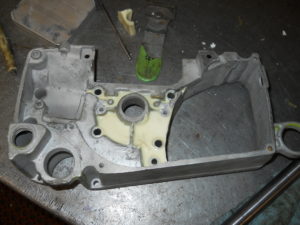
I then removed scallops from the cheeks in preparation of balancing the crankshaft.
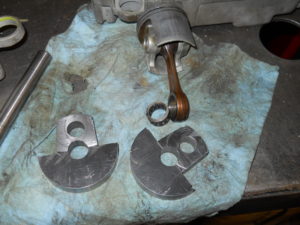
At this period of the project, I neglected photographing some of the process. I painted the case halves. Weighed reciprocating mass and removed material from the cheeks to balance the crankshaft. I trued up the crankshaft, welded it and re-trued it up. Runout is less than .003″. For comparison, a new chicom crankshaft measures .003″
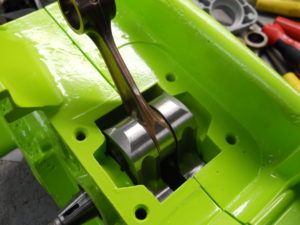
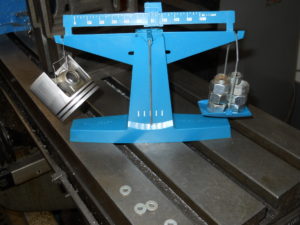
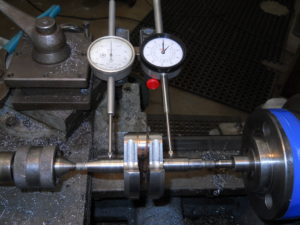
Instead of the original connecting rod, I used a connecting rod from a Husqvarna 395XP. I needed a longer connecting rod with a larger wrist pin bore. This allowed me to use a 56mm piston and cylinder. Displacement has gone from 56cc to 102cc. I made a spacer block to accommodate the larger cylinder.
I started by filling the existing mounting holes with threaded aluminum rod.
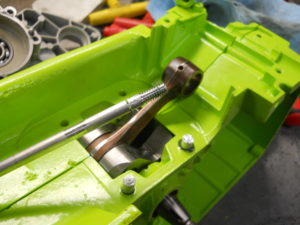
I then milled off the stubs, located, drilled and tapped the new mounting holes.
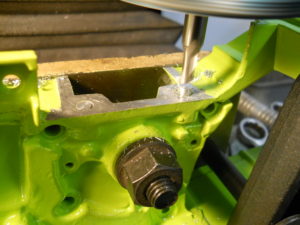
Then I made a spacer to adapt the two different bolt patterns.
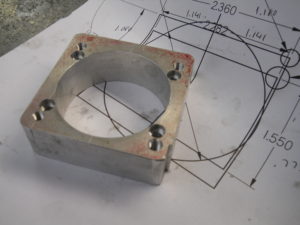
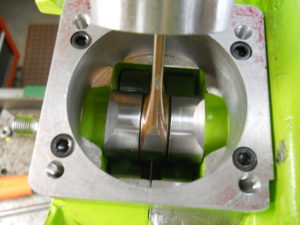
The original carburetor was too small. Also needed was a carb mounting block.
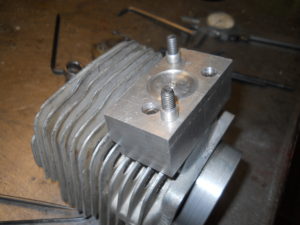
The used 56mm cylinder for this project has damage to the bore near the top where the piston rings stop. I raised the mounting of cylinder to prevent the piston rings from contacting the damaged area of the bore. To maintain compression and performance, I cut the head off of the cylinder and made a removable cylinder head.
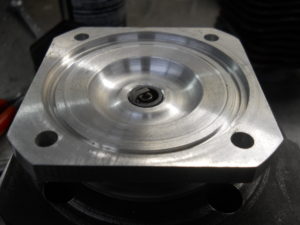
I fitted a larger carburetor, modified muffler and assembled the saw. I had to make a 1/2″spacer to fit the covers. It looks pretty close to stock.
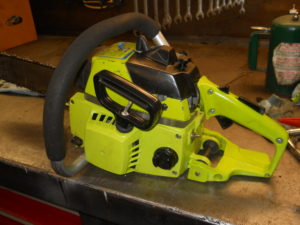
It runs good.
It isn’t finished yet. I have better covers, new decals to put on it. Also, it will be ported for better performance.
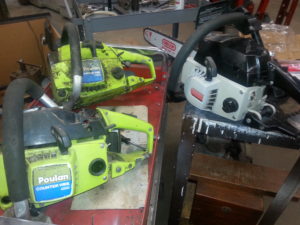